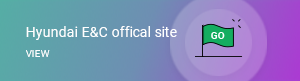
Bags made from abandoned tents and accessories made from recycled materials are trending. In winter, so-called ‘good jumpers’ with renewable wadding were also sold in large numbers. This reflects the preferences of the MZ generation, who are leading the way in consumption trends. They are concerned about serious environmental issues and actively express their beliefs through conscious consumption, also referred to as 'meaning out'.
[ With Gen MZ's ‘meaning out’ trend, reducing disposable products is becoming a way of life ]
With the ever-growing number of cafes that don't use plastic straws, paper cups, or increased use of personal tumblers, it's clear that going green has become a part of everyday life. Going green is not an option but a must. Businesses are also joining the social movement and are actively responding to climate change by producing carbon-lowering products or using recycled materials. Construction is no exception. Hyundai E&C is making ripples in the industry with its innovative recycling practices, and here's the story of Hyundai E&C that truly cares about solving environmental problems than anyone else.
◆Recycling in Nature with Beautiful Harmony
[Hyundai E&CX Hyundai Motor] Monument with Used Car Plastics
Inside the Illumistate apartment complex in Bucheon, Gyeonggi-do, there is an unusual sculpture that catches everyone's attention. It's a seating wall where residents can sit and relax for a while, but there's a twist. The H Wave Bench is made from used plastics collected from Hyundai Motor's R&D process. As the name "Wave" suggests, it's an atypically curved piece that has been transformed into a more sensual installation by Professor Kim Ki-hyun of the Korea National University of Arts in Seoul, South Korea. This amazing transformation was made possible thanks to 3D printed recycled plastic mold.
Bucheon Illuminate's 'H Wave Bench' was completed by pouring ultra-high performance concrete (UHPC) into a 3D-printed mold made from 10,000 500ml plastic bottles, and the introduction of cutting-edge technology has led to the emergence of green product. Hyundai E&C became the first Korean construction company to win the Green Good Design Award 2023 in the 'Product and Graphic Category' for this installation. It is an exceptional case of sustainability and innovation recognized for its aesthetic beauty as well.
Even in the lush greenery of the Seoul Botanical Garden, there is an eye-catching red bench. It's a brilliant work by Hyundai E&C that utilizes plastics from Hyundai Motor’s R&D process. In 2020, Hyundai E&C installed the first 3D-printed H Weaving Bench in an apartment building in Korea, which has awarded the Q mark, a technology patent, and an international design award.
While it is difficult to realize precise shapes with conventional manufacturing methods using concrete, steel, and other materials, the composite material 3D printing technology developed by Hyundai E&C has the advantage of producing various free-curved segments. Thanks to this, used plastics can be transformed into a bench with a sophisticated and fluid design. The bench, which was donated to the Seoul Botanical Garden as part of Hyundai's social contribution campaign 'Longest Run 2022', serves as a beautiful part of the landscape while conveying the meaning of upcycling to park visitors.
So, how much recycled plastics were used in this piece of work? This red bench, which has no apparent signs of waste, contains about 600 kilograms of plastic. Recycling this much plastic results in an estimated 1.036 tons of carbon savings,* and it's amazing to see plastic transformed into something useful and beautiful.
* Based on the U.S. Environmental Protection Agency (EPA) Waste Reduction Model, November 2020.
[Hyundai E&C x Amorepacific] A Shimmering Façade Made from Empty Cosmetic Bottles
Hillstate Pohang's 'H Wave Wall' evokes the shimmering sand of the beach. The wave-motif design and pastel colors highlight the colors of the local area adjacent to the sea, earning it the title of Winner at the Asia Design Prize 2023.
The shimmering, seaside shell-like parts of the H Wave Wall are actually cosmetic bottles. Hyundai E&C has signed an agreement with Amorepacific to utilize empty cosmetic bottles as construction materials. The discarded bottles are mixed with ultra-high performance concrete (UHPC) and turned into architectural terrazzo tiles. Currently, the process has been applied to the walls of the Tea House at Hillstate at Suji-gu Office Station and Hillstate Prugio Suwon, and the total number of cosmetic bottles used is about 286,401, which is an impressive record.
◆ Innovative recycling hidden in construction materials
[Hyundai E&C X Hyundai Steel] Cement Replaced by Carbon-lowering Materials
[ Cement, one of the most common construction materials, is regarded as a cause of global warming because it generates a lot of carbon dioxide during its production and consumption. Hyundai E&C initiated research on alternative materials to cement in 2017, and as a result, came up with a plan to utilize steel byproducts ]
Cement, one of the key construction materials, is regarded an important cause of global warming because it generates a lot of carbon dioxide during its production and use. Cement used in construction sites is known to emit about 0.8 to 0.9 tons of carbon dioxide per ton produced, and according to a recent announcement by the construction sector, it is estimated that about 50 million tons of cement are consumed by domestic construction sites annually, resulting in more than 40 million tons of carbon emissions. Therefore, efforts have been made by the construction sector to reduce the use of raw materials with high carbon emissions during the construction process. Hyundai E&C has also been focusing on developing eco-friendly materials to replace existing cement for a long time.
Reducing the amount of cement used is the key, especially in the case of concrete, which is made by mixing cement and aggregates. So Hyundai E&C began researching cement substitute materials using industrial byproducts in 2017, and as a result 'H-ment' was born. Hyundai E&C's focus was to utilize the byproducts of Hyundai Steel, where slag, an oxide that remains at the top of the blast furnace in addition to the molten iron at the bottom, is powdered and used in concrete instead of cement.
In fact, Hyundai E&C is not the first to develop a low-carbon cement utilizing steel slag. However, what makes H-ment unique is that it has a higher proportion of slag than conventional slag cements, yet it maintains a uniform quality and compensates for disadvantages such as the initial loss of strength in concrete.
There are two types of H-ment: the ‘entry-level’ type, which increases the initial strength by up to 21% compared to conventional slag cement, and the ‘low-exothermic’ type, which reduces the heat of hydration (heat generated when water is added to cement) so that it can reliably prevent concrete cracking due to temperature. In particular, the low-exothermic H-ment was developed to reduce the temperature rise by 9% so that the amount of slag can be increased by 60% without any problem in strength. As the amount of slag used increases, the carbon footprint naturally decreases. H-Ment is said to be 35% less carbon intensive than conventional slag cement.
Piles also play an important role in transmitting the load to the ground to make the structure stronger. Hyundai E&C has developed a ‘Pretensioned spun High-strength Concrete’ pile that replaces cement with slag powder from the steelmaking process. It has higher strength than conventional piles while reducing carbon dioxide emissions by 16%. The pile was recognized as a green technology by the Ministry of Land, Infrastructure, and Transport because it uses 40% slag powder instead of cement used in traditional ultra-high-strength PHC piles, while performing equally well.
[Hyundai E&C X Hyundai Steel] Hardening Soft Ground Using Steel Byproduct: Natural Solidifying Agent
There's another technology that utilizes steel byproducts. It's a technology for making solidifying materials to harden the ground. Solidifying agent is a cement-like material used to harden soft soils when building structures. As mentioned earlier, cement produces a lot of carbon dioxide, and when it comes into contact with seawater, it impacts the environment, so it has long been necessary to develop an eco-friendly solidifying agent.
Hyundai E&C has been successful in developing an eco-friendly solidifying agent manufacturing technology that utilizes steel byproduct, 'sodium bicarbonate'* desulfurization dust' (dust generated during the process of removing sulfur from materials using sodium bicarbonate). The technology, which received green technology certification in July 2020, is eco-friendly by reducing risks and harm to the marine ecosystem and has proven its technical excellence in reinforcing the ground. Following a trial application at the Incheon New Port hinterland complex, Hyundai E&C plans to use it in the ongoing Gwangyang Port Dredged Soil Dumping Site construction project. It is expected to be used for various marine applications in the future.
*Sodium bicarbonate is also called bicarbonate of soda and is more commonly known as baking soda.
[Hyundai E&C x Holcim] Global Collaboration to Develop Low-Carbon Construction Materials
Last May, Hyundai E&C signed an MOU for joint development of low-carbon construction materials and technology cooperation with Holcim, a Swiss-based global leader in green construction materials.
Hyundai E&C's commitment to green materials now extends into global cooperation. On May 24, Hyundai E&C signed a MOU with Holcim, a global leader in green construction materials, to jointly develop low-carbon construction materials and engage in technical cooperation. Holcim, based in Switzerland and France, has more than 1,500 valid patents for green cement and concrete to lead the way in decarbonization. Together with Holcim, Hyundai E&C will conduct research to realize carbon neutrality, including the development of new, low-carbon materials using calcined clay and the development of high-durability concrete technology for the marine environment. The synergy between the two companies, which are both committed to the environment and durable construction, is highly anticipated.
◆ Recycling to Enhance Quality of Life
[Hyundai E&C X Hyundai Steel] Development of High Performance Flooring Utilizing Slag to Reduce Inter-floor Noise
Inter-floor noise has emerged as a cause of neighbors' quarrels, discord, thus a serious social problem. Did you know that Hyundai E&C's technology for controlling inter-floor noise also values care for the environment?
Inter-floor noise is the sound perceived in the air when the floor and walls vibrate due to the impact on the floor. The key to reducing this noise is to reduce the sound of weight impact. High-performance cushioning materials and high-density mortar play a key role. Hyundai E&C has successfully developed a high-performance mortar using slag aggregate, proving its distinctive technology.
Hyundai E&C's 'H Silent Home System' is equipped with high-performance cushioning materials and mortar that reduce inter-floor noise, making the company the first Korean builder to receive Grade 1 certification for both heavy and light impact sound (37 dB or less). The high-performance mortar reduces inter-floor noise via a change in the vibration characteristics by increasing the mass of the existing Ondol layer by recycling slag aggregate. Slag aggregate is heavier than ordinary sand, so it is possible to develop a high-density Ondol layer.
[Hyundai E&C X Hyundai-Kia Motors, Hyundai Steel] World's First Eco-friendly Road Pavement Utilizing Automotive Waste Parts and Slag Aggregate
[ Hyundai E&C is leading the way in improving environmental issues while boosting performance by utilizing waste automobile glass and slag for asphalt used in road paving ]
What if the road was littered with shards of glass? The thought of it makes you dizzy, but did you know that there are roads that are made of scrap glass from cars?
Hyundai E&C has developed a road paving method that utilizes waste parts such as polyvinyl butyral (PVB) used in Hyundai vehicles as construction materials. Asphalt pavement is done using aggregate, powder, and an asphalt binder that binds them together, and since waste glass is used instead of natural limestone powder, it is a highly economical process that does not harm nature and reduces waste disposal and raw material costs.
In particular, Hyundai E&C's green asphalt paving method is made possible by adding – PVB (which is used as an adhesive for automobile double-glazing) and rubber around the door to the asphalt, so that it can be produced and constructed at medium temperatures. It can be produced at 120 to 130 degrees, which is about 30 degrees lower than road pavements that are usually produced at 150 to 160 degrees, resulting in fuel savings of about 30 percent and a reduction in carbon dioxide generation. In addition, the asphalt performance has also been enhanced. Compared to ordinary pavement, it is less prone to wavy deformation and cracks that cause the road to split, and it is stable in high (76 degrees) and low (-22 degrees) temperatures, making it possible to use it in hazardous sections such as roads with high traffic and intersections.
That's not all. The aggregate used for pavement also has the advantage of not causing environmental pollution, as slag from the iron making process is utilized to develop stone mines for the use of natural aggregates. These slag aggregates are harder than natural aggregates and, like basalt, have pores that allow the asphalt to be absorbed well, providing excellent binding. This is the world's first challenge to use all materials, including fill and aggregate, as waste materials! We look forward to the commercialization of Hyundai E&C's green road pavement method, which is not only economical but also environmentally friendly.
The various constructions that Hyundai E&C erect are filled with the company’s genuine care for people and the environment, from the smallest details that are invisible to the largest ones that can be seen. This commitment has been realized through innovative technology development and is constantly evolving. Moreover, as the demand for carbon neutrality in the global construction market expands, construction materials that can meet high performance, high-quality and low-carbon and eco-friendly requirements are gaining prominence as core competitiveness for construction companies.
Construction is vital for human comfort and safety. Hyundai E&C believes in harmonizing the environment and people, and strives for construction that does not harm nature and instills freshness into its pristine beauty. Such commitment is evident in the fact that Hyundai E&C was the first listed construction company in Korea to declare 'Net Zero by 2045' initiative and publish a Net Zero Report containing its net zero goals and plans.
Looking ahead, Hyundai E&C will continue to build a sustainable tomorrow by developing technologies that will greatly benefit the future generations and the world.