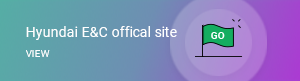
Experience itself is a powerful weapon, especially the experience of someone who has been committed to one specialty. One of the key reasons how Hyundai Engineering and Construction (Hyundai E&C) came to its position on the global stage is because of the people who trained themselves for a long time to become experts in their respective fields. Hyundai E&C writes a special feature based on interviews with in-house experts, who have been at the core of the company’s competitiveness.
Hyundai E&C’s expert nuclear welder Senior Manager Kim Jeong-heon
“The secret to constructing safer nuclear power plants lies in the quality of welding”
[ UAE Barakah nuclear power plant is the first overseas nuclear power plant project Hyundai E&C won over prestigious competitors of France, the U.S., and Japan. ]
Korea is a nuclear powerhouse. There are 24 reactors currently operating in Korea, while 2 have been discontinued due to obsolescence and 4 new ones are being built. The country also has a proud achievement of exporting nuclear power plants. Winning the fierce competition against companies in France, the U.S., and Japan, Korea won the UAE Barakah nuclear power plant project in 2009. This project made Korea the 6th nuclear exporter in the world. And it would be disheartening to leave out Hyundai E&C when talking about the country’s huge achievement. Starting with Korea’s first-ever nuclear power plant, Kori 1, in 1978, Hyundai E&C participated in the construction of 22 out of 34 large-scale Korean nuclear power plants at home and abroad. As such, Hyundai E&C has the most performance record in the construction of nuclear power plants as well as exporting experience among all construction companies in Korea.
The company boasts its outstanding technology in nuclear power plant construction and there are many experts in the field of nuclear power plants with longstanding experience and ability. Senior Manager Kim Jeong-heon of Nuclear Energy Sub-Division is one of them. Senior Manager Kim, who is a core member in the field of nuclear technology management at Hyundai E&C, is also known as the ‘nuclear welding expert’ inside and outside the company. He is a mentor to many welders on-site. Let’s meet Kim Jeong-heon, who has not only expertise on nuclear power, but also acumen based on experience.
Spearheading the ‘introduction of automatic welding’ for the first time in Korea
“Current time is 6:30 in the morning, so that makes it 11:30 a.m. in Korea. Good morning, I am Senior Manager Kim Jeong-heon at Nuclear Energy Execution Supporting Team. I am here at the site of the Barakah nuclear power plant, located 270km west from UAE’s capital, Abu Dhabi. I’m here on a business trip to provide technical support to improve the performance of the on-site ventilation system of Physical Protection System (PPS)*. I worked as a technical manager here from 2014 to September last year, so I’m working without any delay.”
*PPS: Physical Protection System that protects key assets and nuclear materials at the nuclear power plant from malicious attack.
[ Senior Manager Kim Jeong-heon in front of a mockup of UAE Barakah nuclear power plant. Kim, who had worked as the site technical manager from 2014 to September last year, visited UAE again to provide technical assistance. ]
“Energy produced with human brain,” is what we say about nuclear energy. It is not a resource from nature, but energy created by the aggregation of technologies. Although nuclear power plant combines a wide range of high-tech technologies, it requires a “human touch”, that is “welding”, to build a nuclear power plant. Kim Jung-heon is a seasoned nuclear power plant expert with more than 24 years of experience in nuclear power plant projects alone. He began working at a nuclear power plant site in 1998 and has worked at five nuclear power plant sites in Korea and abroad, including the construction of 1 to 4 units of the Baraka nuclear power plant in UAE> In September last year, Kim returned to the Nuclear Power Plant Division at Hyundai E&C headquarters to work on nuclear decommissioning and spent nuclear fuel operations. Although Kim has a lot of knowledge about nuclear power plants, his specialty is welding. While working as a technical manager at nuclear power plant sites, he learned that many questions coming from * Korea Institute of Nuclear Safety (KINS), operating and supervisory body of nuclear power plant construction, were about welding. So, he decided to study to build relevant expertise.
* Korea Institute of Nuclear Safety is a public institution under the Nuclear Safety And Security Commission that regulates nuclear safety operations and manages and supervises compliance of nuclear power plant constructors.
“Realizing that nuclear power plant safety depends on the quality of welding, I acquired the highest qualification in welding in 2004. Although it was difficult to pass the first round known for its success rate of only 12.6%, I studied day and night thinking about countless welding questions I received on site. I vowed to make what I studied throughout the exam period into living knowledge. I believed that no matter how I excelled in theory, I should be able to put my knowledge into practice.”
Kim Jung-heon’s sense of responsibility soon made his resolution a reality. Thanks to Kim, Hyundai E&C became the first Korean builder to successfully introduce ‘automatic welding on the piping of reactor coolants’. Nuclear power plants are divided into primary *systems and secondary systems. The primary system consists of nuclear reactors and coolant pumps, piping, and steam generators, which are the most important equipment in nuclear power plants. The secondary system is an instrument related to a turbine generator, whereby electricity is produced and steam is converted to water. The reactor coolant piping of the primary system is the core of the nuclear power plant, connecting the reactor-steam generator-coolant pump. Automatic welding had once been applied to the steam generator replacement works, but due to high-level technology, the work was led by specialized firms from abroad, and not Korea.
* A system refers to components being inter-related according to a specific structure.
[ A nuclear power plant has primary systems and secondary systems. The primary system consists of the most important equipment at a nuclear power plant such as the reactor, coolant pumps and piping, and steam generators, while the secondary system consists of equipment related to turbine generators. ]
When Senior Manager Kim worked as a technical engineer at the Shin Kori nuclear power plant reactors 1 and 2, he started pretesting* and technology development with the construction department to apply automatic welding on the piping of reactor coolants. And in 2008, he successfully introduced automatic welding. This allowed the team to shorten the construction period from 7 months to 5.5 months. At the time, various media outlets reported, “introducing the new method reduces construction period, and therefore improves economic feasibility.” Kim also commented, “we are very proud to be the first construction company to introduce automatic welding in the core system of a nuclear power plant.”
*A mock-up test under the same conductions of the site.
[ Automatic welding requires testing before deployment to ensure consistent welding quality. The welding machine moves according to the estimated value when you input expected welding variables (current, voltage, weaving speed, etc.) into the controller. Welders check and monitor the process through the screen. Image shows testing to develop the variants that will apply in the automatic welding. ]
“I feel extremely rewarded when I see my expertise come to life on site. Narrowing the gap between theory and reality requires knowledge and expertise on not only welding, but also piping, machine, and construction. We must carefully understand the challenges faced by construction managers and welders, any issues on site, and potential problems. Because of the effort I make, our clients and auditing agency trust my opinion. I think that positive feedback is what keeps me going (laugh).”
Hyundai E&C’s nuclear welding quality management that is recognized at home and abroad… Enhancing K-nuclear’s status through ‘technology of the fingertips’
Hyundai E&C, which has the best nuclear power plant construction achievements in Korea, also boasts world class-level nuclear welding technology. Its welding quality management process is recognized for its excellence at home and abroad. The quality of welding is defined by various elements such as the welder’s skill, surrounding environment and condition, pre-heating, variants related to weaving*, post-heating*, and heat input*. Among them, current and voltage control as well as weaving speed are related to the welder’s skill and ability.
*Weaving: the way the welding rod moves
*Post-heating: heating the parent metal (the base metal that you are welding on) after welding or gas cutting.
*Heat input: the amount of heat supplied to a weld. Heat input increases when current and voltage is high. If weaving speed if fast, it remains on the weld less, meaning that the heat input is lower. Excessive heat input must be managed closely as it may cause intergranular corrosion (form of corrosion where the boundaries of crystallites are more susceptible to corrosion) cracking or reduced toughness (resistance of the material to outside impact).
Any contract in a nuclear power plant project stipulates matters on welding quality management and welder management. Even after breaking ground, we submit a monthly report on the management status. Automatic welding is being introduced gradually, but various types and methods of welding are needed on site depending on the construction process. And therefore, the experience and expertise of the welder is important. Advanced countries in the West such as the U.S. and France are seeing a rise in demand for nuclear power, which is shining a light on the importance of fostering welding engineers. In fact, on June 23 (local time), the Wall Street Journal reported that construction is being delayed in some of the nuclear power plant projects in the U.S. and Europe due to issues with incomplete welding. In France, they identified about 100 problems near the cooling system of Europe’s next-generation pressurized water reactor, delaying the project by more than 10 years. Welding engineers are conducting maintenance work, but it is said that the quality of welding is significantly lower than expectation. There was also a case in the U.S. where an issue with welding caused a halt in the construction of a nuclear power plant for quite some time. The Wall Street Journal commented that these problems are due to not investing in training new engineers because the countries have stopped investing in nuclear power for decades.
“Hyundai E&C boasts excellent human resources. Our competitors as well as our clients envy us for that. Our company continued to carry out nuclear power plant projects. As a result, our in-house nuclear experts had the opportunity to gain experience. And the ideas and solutions that came out of that experience are what made Hyundai E&C outstanding. Companies with relatively less experience develop their operation plan referring to Hyundai E&C’s welding quality management process.”
[ Welding engineers receiving technical training at Hyundai E&C’s nuclear welding school. ]
Since the 1970s, Hyundai E&C ran welding schools customized to each nuclear power plant. While he was working at the Barakah nuclear power plant, Senior Manager Kim Jeong-heon taught engineers theory and skills and inspected and supervised whether they fulfilled their qualifications. This mega project that is the equivalent to four times the size of Yeouido (8km in width, 1.8km in length) produced 2,100 welders of diverse nationalities. Considering that there are around 500 welders with qualifications per one nuclear power plant in Korea, this is a significant number.
“I tried to help welders understand the welding system of the Barakah nuclear power plant as well as to have the ‘right mindset’ when it comes to welding. This mindset includes not only the engineer’s skill and ability, but also to ensure no safety accidents occur and to comply with the rules. Hyundai E&C’s unrivaled welding management process and knowhows received huge response on site as well. Our client, Emirates Nuclear Energy Corporation (ENEC), sought out consultation on establishing a welding training center at the power plant. They also learned the structure and how Hyundai E&C’s welding schools are managed.”
The course one has to take to work as a welding engineer at a nuclear power plant is quite complex. Engineers have to receive at least three months of training at a welding school. They also require more than one or two years of experience to be a fully skilled welding engineer even after getting the right qualifications.
“The temperature, heat input around the weld as well as speed determine the quality of welding. If the heat input is too high or too low when welding iron pipes or plates, the steel melts down and it won’t weld. The secret to becoming a skilled welder is to learn how to improve quality by adjusting these elements throughout the process. Individual welders work with a different scope of acceptable variants that they prefer. So, the role of an instructor at a welding school is to help promising engineers work within defined scope through education and training. A structured training program and thorough management makes the difference in skills. And this is what determines the competitiveness of a company in the nuclear sector.”
Selection of nuclear welders | ‧ Examination of skills per welder ‧ Training on on-site welding policies ‧ Internal testing and theoretical examination |
Qualification test ※ Hyundai E&C and project owners (KEPCO, ENEC) quality manager’s presence mandatory | ‧ Practical examination : Comprehensive test of welding skills, welding rod management, preparation before work, compliance during work, and post-process after welding ‧ Nuclear welding qualification granted and welding qualification card issued when welders pass all tests |
On-site welding management | ‧ Monitoring appropriate work amount per welder through on-site inspection ‧ Welding quality management through non-destructive testing every month ‧ Training on-site for any inadequacies discovered |
※ Re-training and disqualification ‧ Retraining up to 8 hours in case intensive training is required ‧ Disqualified if written up more than 3 times |
[ ‘Hyundai E&C welding school curriculum’ has become the standard at nuclear power plants at home and abroad. Hyundai E&C has unparalleled management knowhow in the field of nuclear welding quality. ]
All documents on welding at the nuclear power plant records the names and IDs of each responsible welder. Before each task, welders fill out a welding rod release form every day and sign their name on the form when returning the rod after every task. Senior Manager Kim Jeong-heon emphasizes to welders, “think back if you have followed the rules and policies on-site, and then sign your name on the release form after final confirmation.”
“I feel a sense of accomplishment when I see beginning welders, who couldn’t be deployed in important tasks the first time they entered the course, start working on primary systems after 1 to 2 years of on-site experience and training. Welders from Southeast Asia such as the Philippines and Vietnam are especially proud to have worked as welders at a nuclear power plant that they even request for a renewed qualifications card as they return home (laugh).”
Developing welding process customized to all nuclear power plants such as SMR
Senior Manager Kim Jeong-heon has worked as a welder for 16 years in Korea and more than 7 years abroad. He knows the unique characteristics of an overseas nuclear power plant as a welder who has experience both at home and abroad. For example, ENEC, owner of the Barakah nuclear power plant, recruited nuclear experts from the U.S. and Europe to supervise the construction and they had different standards to Korea. Quantitative standards were acceptable, but there were times it was difficult to understand their qualitative judgements. Senior Manager Kim said, “I learned a lot while working at the Barakah nuclear power plant.”
[ Since obtaining his Professional Engineer Welding qualification in 2014, Senior Manager Kim Jeong-heon has worked as an expert in nuclear power plant and welding. ]
“Even our company, which has extraordinary knowhows on nuclear power plant construction, can’t always work the way we are familiar with. In the future, finding common ground with different clients will be key in construction projects especially in overseas nuclear power plant projects. Hyundai E&C is creating a database based on the successes and failures and knowledge so that the valuable experience on site become our strong asset. I believe that the database will be a great asset in future overseas nuclear power plant projects.”
Hyundai E&C has established a management system across the entire areas of nuclear power generation such as small modular reactors (SMRs), nuclear dismantling, and processing of used nuclear fuel, based on its large-scale nuclear power plant projects that were recognized globally for their competitiveness. The company is especially focusing its capability on integrated SMRs including reactors, steam generators, coolant pumps, and pressurizers. Senior Manager Kim explained, “there’s a difference in design, but the technical standards and welding methods are similar to that of a large-scale nuclear power plant” and added, “we are developing a welding process customized to SMR.”
“Hyundai E&C has welding processes for all structures and components required in a nuclear power plant such as containment liner plate (CLP)*, reactor coolant system, and spent fuel pool. We aim to develop them further to apply them to SMR-160* and future overseas projects. I am currently a member of the subcommittee in machinery of the Korea Electric Power Industry Code (KEPIC)*. The committee delivers expert opinion on nuclear quality assurance qualifications (KEPIC-MN) and proposes technology to apply to new nuclear power plant projects. I will do my best so that Hyundai E&C can deliver outstanding performance in the field of nuclear power plants and welding quality management. And I will continue my effort in fostering future talent so that we have more in-house experts on nuclear power plants. I ask for your continued encouragement and support!”
*There is a ‘liner plate’ installed along the inside of a reactor containment building. The liner plate contains the building so that it doesn’t leak.
*SMR-160: a 160MW-grade light-water SMR that Hyundai E&C is jointly developing with Holtec International, one of the best companies in the field of energy and nuclear in the U.S., that can be deployed without regional or environmental restrictions such as in deserts or extreme regions.
*Korea Electric Power Industry Code (KEPIC): standards of private organizations for the energy industry that stipulate methods and procedures regarding nuclear power plants, thermal power stations, the safety of equipment and devices including power transmitters, transformers, and distribution facilities, and design, manufacturing, construction, operation, maintenance, testing and inspection for reliability and quality assurance.