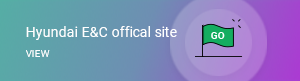
Another masterpiece across the Han River: a concrete cable-stayed bridge with the world’s longest span
A concrete cable-stayed bridge is being constructed in Gangdong-gu, the eastern district of the Han River, in harmony with the surrounding scenery. As part of the Sejong-Pocheon Expressway (14th Section) project connecting Anseong and Guri, Hyundai E&C is working on the construction of the tentatively named Godeok Bridge. It is the 33rd bridge across the major river flowing through the heart of Seoul and the 14th in the river constructed by Hyundai E&C.
The Sejong-Pocheon Expressway project was designed to resolve traffic congestion in the Gyeongbu Expressway and the Jungbu Expressway. These two highways linking north and south of the country have not functioned properly due to severe traffic congestion. The Sejong-Pocheon Expressway is expected to solve chronic traffic congestion in the existing expressways as well as play an important role as not only a key traffic network connecting Sejong-si, de facto administrative capital of the country, and the capital area but also the main artery of the national economy.
The 128.1-kilometer Sejong-Pocheon Expressway project, valued at 9.6 trillion won, includes three sections such as the 21.9-kilometer Guri-Seongnam section, the 50.3-kilometer Seongnam-Anseong section, and the 55.9-kilometer Anseong-Sejong section. The mega-sized project started from the Guri-Seongnam section. Among them, bidding companies scrambled to win the 14th Section aimed at building the 2.04-kilometer Anseong-Guri section with a focus on bridge construction. The successful bidder was chosen on a “design-to-cost” basis, the first of its kind in the domestic construction market. In the design-to-cost methodology, technological competitiveness plays the only role in selecting the successful bidder at fixed bidding prices without competition over prices, which means that bridge design technology was a key to winning the project. Hyundai E&C successfully won the deal by suggesting the construction design for the concrete cable-stayed bridge with the world’s longest span with an aim to minimize the number of towers and increase the distances between them to prevent environmental damages to the river.
[The form traveller used to produce four-meter decks]
The Sejong-Pocheon Expressway (14th Section) project started the construction in December 2016. Construction of temporary facilities was completed in 2017, and foundation work was finished in 2018. After the commencement of construction of towers the same year, the construction site is currently working on concrete bridge decks and cables. As of April 21, 2021, 57.95 percent of the project was completed, and the construction site is making its all-out efforts to successfully finish the project by December 2022.
“Smart” technological cooperation between project site and head office
The Sejong-Pocheon Expressway (14th Section) project includes the construction of 16 bridges and two interchanges, along with the Godeok Bridge with a central span of 1,000 meters and the 725-meter approach bridge. Notably, the Godeok Bridge is constructed as a concrete cable-stayed bridge with a 540-meter-long span between towers, which is the longest in the world.
To build the Godeok Bridge on a global scale, Hyundai E&C introduced cutting-edge smart construction technologies and promoted cooperation of varying types among the construction site, the head office and researchers from various fields. For example, ultra-strength concrete and cables were needed to build the concrete cable-stayed bridge with a long span between two towers. To this end, the design standards for cable-stayed bridges and 2,160 MPa-grade PS strands were applied, the research results of the Super Long Span Bridge R&D Center of Korea Expressway Corporation in which researchers from Hyundai E&C and various industries participate.
[Concrete placement for stiffened decks]
Staff working at the construction site and the Infrastructure Competitiveness Team in the head office made outstanding efforts to cooperate in the application of high-strength concrete, the first of its kind in the domestic construction industry. To maintain bridge alignment, it is significant to manage displacement of bridge structures in each construction stage. In each phase of construction, the high-precision GPS system, one of smart construction technologies, was utilized to minimize measurement errors, and stiffened decks were built at targeted spots by modifying tension of relevant cables.
Notably, an advanced technology was utilized to transport and place 80 MPa-grade high-strength concrete to superstructure. To achieve better-quality construction, the project site fabricated stiffened decks at an actual size of a bridge segment prior to the construction, and conducted a test for long-distance concrete placement through piping. In addition, the close cooperation between the project site and the Infrastructure Competitiveness Team enabled the introduction of the “smart concrete curing management system” designed to forecast concrete strength based on concrete curing temperature. The new system is currently being test-operated and will be applied this summer.
[The ACS (Auto Climbing System) introduced to build bridge pylons. In the ACS, forms are automatically pushed upward without their dismantlement and reinstallation, which makes it easy to manage construction quality and improves work efficiency]
These all-encompassing efforts allowed the Godoek Bridge to obtain seismic resistance with a return period of 4,800 years and wind-resistant safety, so that the bridge can resist wind velocity of 100 m/s or higher.
On top of this, BIM (Building Information Modeling) technology was introduced to the entire construction process, the first among domestic expressway projects. BIM refers to a system which helps users integrate all building information based on three-dimensional design methods. This project attempted at applying the BIM system to the entire process ranging from designing to construction and maintenance.
“When unexpected incidents sometimes occur during construction processes, the use of BIM system enables users to review complex designs in a three dimensional way, which helps prevent risks from taking place in the first place,” said an official of the construction site. “The BIM technology has considerably improved constructability and construction safety.”
Workers also welcome the use of BIM, saying that it is easier to understand 3D floor plans compared to 2D ones. Once the construction of the Godeok Bridge is completed, the BIM-related data on the entire construction process will be integrated and stored into a digital twin framework. The accumulated information will increase the capability of Hyundai E&C to build highway bridges and utilize smart construction technologies.
Smart safety management leads to zero major accidents
Safety management was conducted in a smart way. One of the most challenging issues facing the construction site was to deal with the water level in the Han River. Torrential downpours could rapidly increase the water level, possibly leading to flood damages. To address this, a text message service was introduced to alarm the quantity of water flow on an hourly basis through a system jointly established with the Han River Flood Control Office. As an effort to cope with possible risks of flood damages, the construction site came up with the emergency evacuation manual and the safety system to respond to changes in the water level in the river.
In addition, the smart safety management system was introduced as well. The construction site applied the AMG (Automated Machine Guidance) system to improve safety of the operation of tower cranes by attaching various sensors and cameras to them. In order to secure safety of those working on the bridge, the Beacon, the location-based signal transmission device, was attached to the workers’ safety helmets to monitor their locations in a real time. Safety training programs were provided to show the site environment based on 3D modeling to workers involving possibly dangerous works. All these safety-related efforts led to achieving zero major accidents.
[Panoramic view of the tentatively named Godeok Bridge, the Sejong-Pocheon Expressway (14th Section) project]
All employees at the construction site expressed their ambition to achieve the world’s best project management and technological capability by saying that they will exert their utmost to lay the foundation for wining further orders to build long span bridges.